Fan Cheng Inside story: Sony automatic chemical plant composed of 32 robots
Published on:2020-07-08
Sony is a world-famous company, and its business covers many fields: TV, mobile phone, game console... Among them, PlayStation (PS) 4 is their representative product. Since the launch of PS in 1994, Sony has won hundreds of millions of fans around the world. But few people know that the success of this game console is largely due to this huge white building across the sea from Tokyo.

▲ the highly automatic chemical plant in mugengjin, which has helped produce all generations of Playstation hardware since PS1 was delivered in 1994
Opposite Tokyo Bay, there is a little-known Sony factory in mugenjin City, Chiba Prefecture. In a 31.4 m x 6 m area, with the motor buzzing, 32 robots are passing on the traditional manufacturing process, and one Playstation (PS) 4 goes offline every 30 seconds. Mugengjin factory is not only an important production base of Sony, but also the location of the game console production think tank team.
It is reported that from this year, Sony will manufacture and produce four different game consoles in two generations of products: PS4, PS4 pro, ps5 and ps5 digital version, so as to maximize production efficiency. In view of the strategic significance of ps5 to Sonys market in the next decade, mugenjin factory will also become another huge asset and competitive chip of Sony.
Sonys cash cow: Playstation
What is the first thing that comes to mind when you hear the name Sony? transistor radio? Walkman? Or robot dog? If you are a loyal supporter of video games, the answer may be Playstation (PS).
Every console is precision manufactured, every part is necessary, every design has its purpose, and PS has no redundant design. Yasuhiro ootori, head of Sonys mechanical design department, once said, "if you pursue technology, mechanical equipment can become an aesthetics."
In 1994, the first PS was born. Through CD-ROM HD video games, Sony overturned Nintendo, which once dominated the home video game market, and PS became Sonys cash cow. In 2008, the collapse of Lehman Brothers caused the financial crisis. Although Sony also suffered a heavy blow, it was PS business that made it survive the crisis.

The Playstation 4 currently produced by mugengjin factory made its debut in 2013. In addition to games, it is also a platform for movies and music, and can even be used for virtual reality games.
Despite the popularity of smartphone app games, the sales volume of PS4 has steadily increased to more than 100 million once it is launched. Compared with its peers, it reached this milestone in the shortest time - a total of about 1.2 billion software sales.
Over the past six and a half years, the PS4 has generated sales of 10 trillion yen ($93 billion) and profits of more than 1 trillion yen. In 2018 and 2019, PS became Sonys highest revenue source, exceeding its revenue in the semiconductor and financial fields.

▲ PS4
Behind the explosion: an automatic chemical plant with 32 robots
Ken Kutaragi, the father of Playstation, pushed the game console despite the opposition of other executives, and finally became the classic of Sony technology today. This is inseparable from the cooperation between Sony global manufacturing & operations (sgmo) and Sony interactive entertainment, the video game department, to continuously introduce cutting-edge technology into the factory.
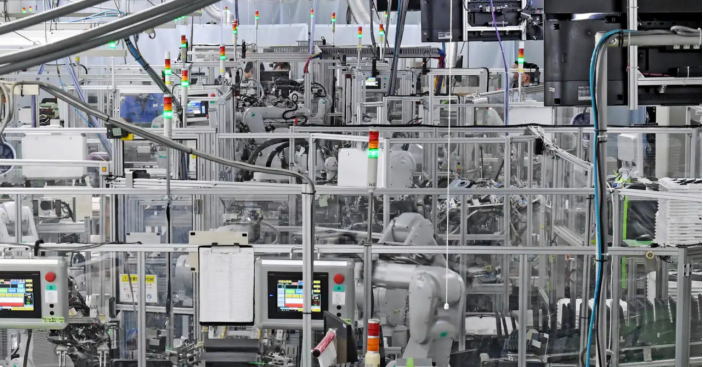
▲ internal conditions of mugengjin factory. Over the years, the factory technology has been continuously improved and transplanted to the factories of global partners
Inside the factory is a 31.4m long production line, which was completed in 2018. Now, a new game console can be produced every 30 seconds. At 31In the area of 0.4m x 6m, a total of 32 Mitsubishi Electric Industrial robots are responsible for most of the production process.
Only four workers on site are responsible for a small number of tasks. They are responsible for transporting the exposed motherboard to the production line. The other two are responsible for packaging and assembling the completed game console.
The bare motherboard is located at the starting point of the whole production line. After being sent to the assembly line by workers, the movement is realized by robots.
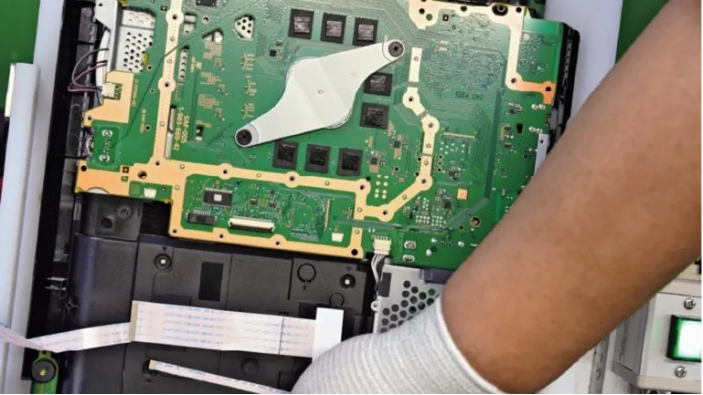
▲ main processor APU surrounded by memory chip
Soon, the white robot arm will appear from both sides of the assembly line and start connecting wires and tightening screws. They kept working like graceful dances.
Initially, the factory arranged more than 80 robots to work. After reviewing each process, they found that it was not practical at all. The current working mode is that a robot constantly repeats its actions from right to left, and cooperates with other robots to complete specific work at each point in the moving process.
They pasted various memos on various surfaces of the production line, such as the lower assembly line and the isolation around the robot. These memos record a lot of trial and error, and finally help the factory realize the automation of the whole process in 2018.
"If you look at them for a long time, they will start to look like humans," an engineer explained to the media. Unlike large robots that lift heavy objects, small robots have fine movements similar to human arms and have temperature, and "there may be no other production base to use these robots so efficiently."
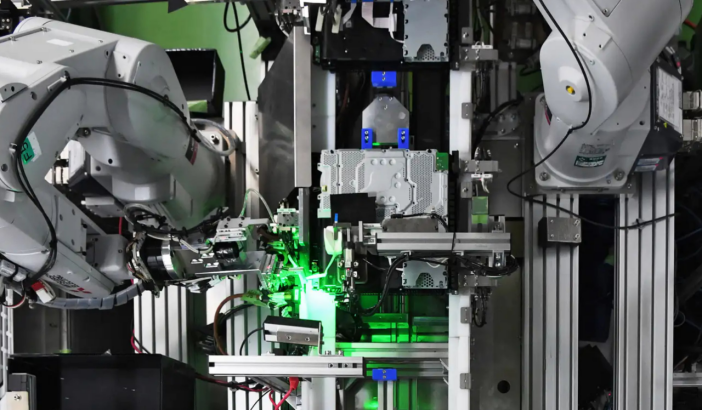
▲ the mainboard is moved by the mechanical arm
Thanks to these talented engineers, the production line can run. However, one of the factorys greatest achievements is the use of robots to connect wires, tape and other flexible parts to the console. You know, one of the biggest obstacles for musk to realize the high automation of Tesla factory is the robots inability to do anything about these soft cables. They even applied for a "structural cable" patent to solve the challenge that robots are not good at wiring, although it is easy for humans.
Of the 32 robots in Sonys factory, 26 are specialized in the installation of soft parts. Sony also designed the PS4 as small as possible so that soft foldable parts can be installed in a small space inside the game console.
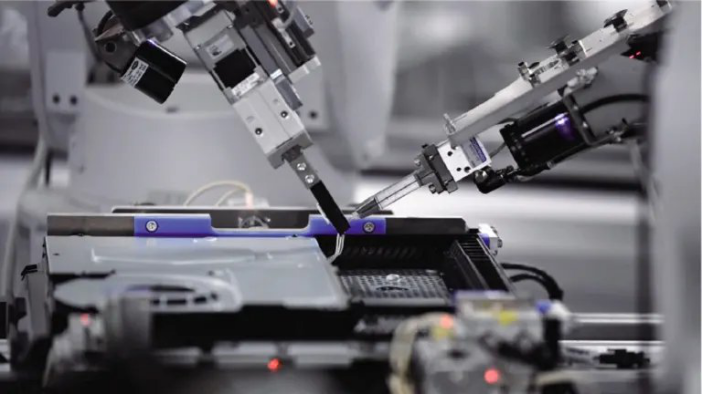
▲ among the 32 robots, 26 are specialized in the assembly of soft parts
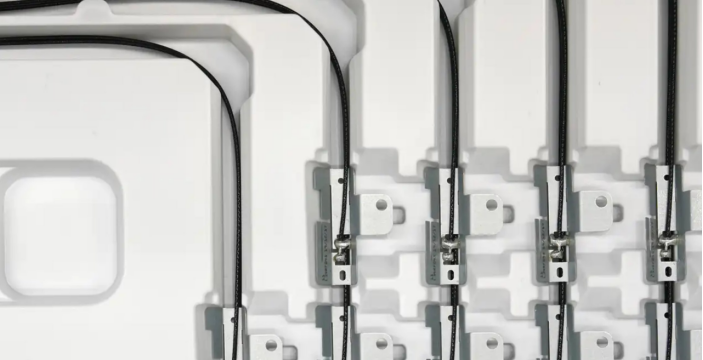
▲ PS4 is composed of many soft parts, such as antenna cable, etc. manual workers are very good at doing these jobs
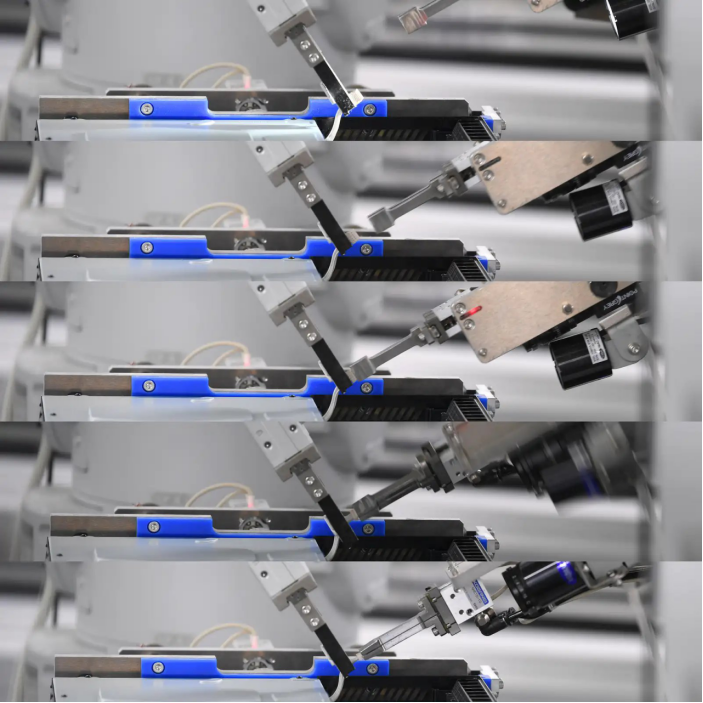
▲ the robot grabs, bends and twists the soft part with slender fingers. Then, slide this part skillfully into the connector with appropriate force
We can see in the disclosed image that one robot arm picks up a cable and holds it, and the other robot arm grabs the tip of the cable, twists it and adjusts the angle, and then puts it into the connector. The whole process emphasizes order and requires strength and precision. Human beings can do this in a short time, but it is an extremely complex operation for robots.
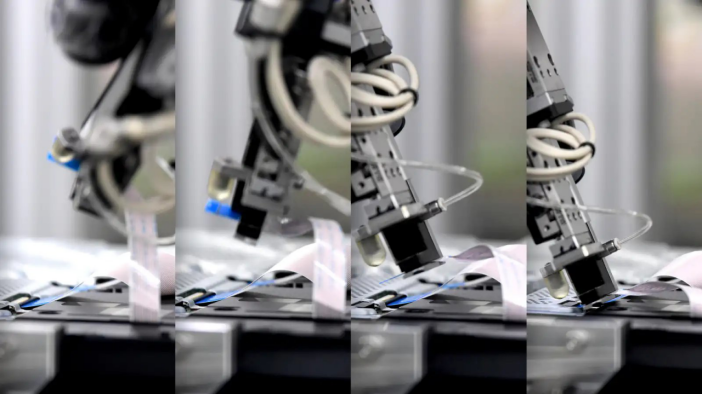
▲ the robot will twist the ribbon cable and install it into the connector
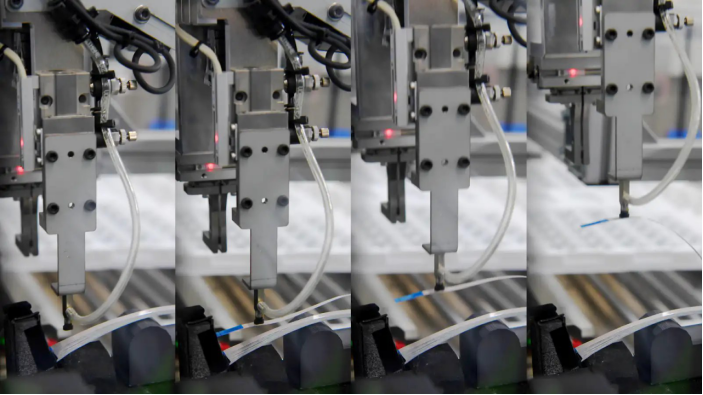
▲ for some parts that are difficult to move and grasp, the robot will first suck them up
After assembly, the assembly line sends the game console to automatic detection.
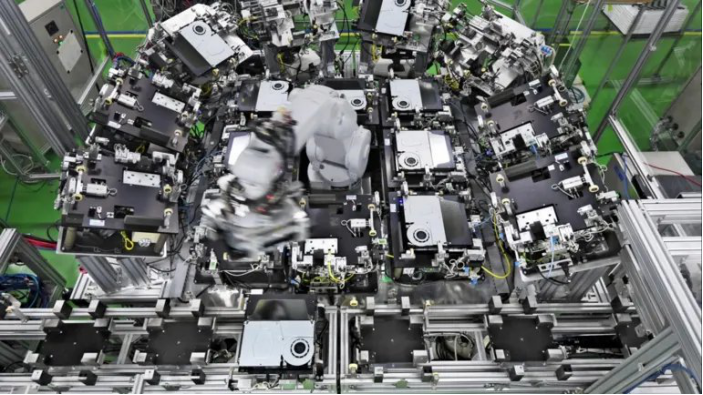
▲ a robot arm grabs the Playstation 4 game console from the assembly line and puts it on a platform for testing
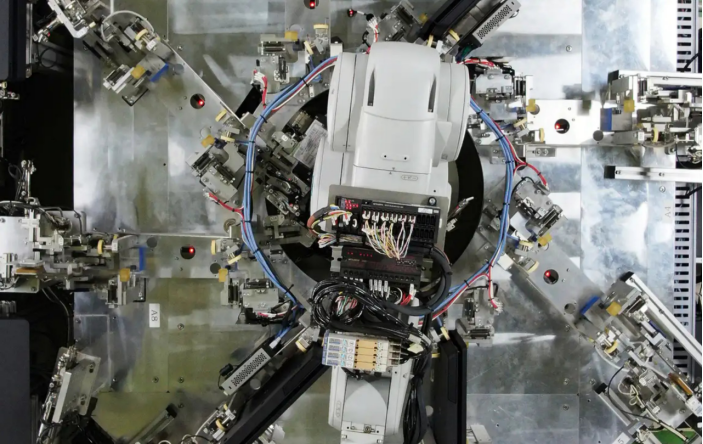
▲ carefully inspect the assembled game console
After the robot carefully checks the PS4, it can be moved away by the machine. Placing the main cover is the last step in PS4 production. The machine grabs one PS4 passing the inspection procedure at a time, puts it on the track and arranges it neatly until the main cover is installed.
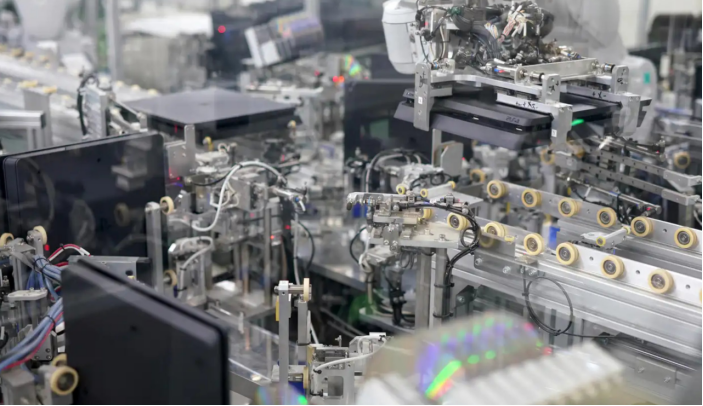
▲ the last step is to place the main engine cover

▲ one PS4 goes offline every 30 seconds
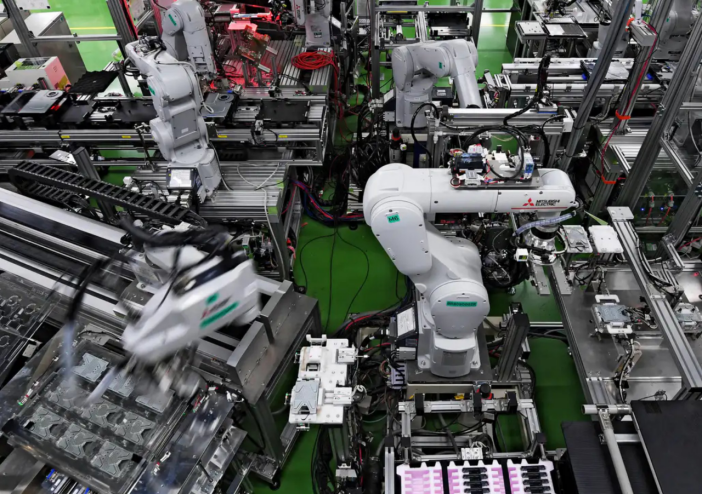
▲ 32 robots seem to work independently, but in fact they are interconnected
Sony manufacturing keeping pace with the times
In addition to the beginning and end, the whole process is highly automated. Sony is enjoying a return on its investment in a reasonable combination of robots and human labor.
"I created a profitable production line," said Hiroyuki Kusakabe, chief architect of sgmo.
When the market life of a game console is coming to an end, it will inevitably become a victim of falling sales and price competition. By continuously improving the production line, accelerating production speed and reducing costs, the production line can remain profitable.
In fact, since Sony launched its first model in 1994, mugenjin factory has carried DNA focusing on productivity. When designing, game console designer teiyu goto focused on creating a game console that is easy to mass produce. He even pushed the engineers in the factory to continuously improve production efficiency, and these fine production technologies were even transplanted to the contract manufacturing factory.

From a larger social and economic background, Sony factorys investment in automation is also to deal with the problems brought by labor costs. Labor cost is still an important chip in competition. In the past, a very important factor to reduce the production cost of these electronic products was to migrate production and manufacturing and obtain cheap labor. For example, in the early 20th century, Sony established close ties with Chinas electronic manufacturing service provider (EMS) to engage in PS production.
However, automation has changed the way companies compete ?, manufacturing itself is becoming the trigger of enterprise innovation.

▲ the highly automatic chemical plant in mugengjin, which has helped produce all generations of Playstation hardware since PS1 was delivered in 1994
Opposite Tokyo Bay, there is a little-known Sony factory in mugenjin City, Chiba Prefecture. In a 31.4 m x 6 m area, with the motor buzzing, 32 robots are passing on the traditional manufacturing process, and one Playstation (PS) 4 goes offline every 30 seconds. Mugengjin factory is not only an important production base of Sony, but also the location of the game console production think tank team.
It is reported that from this year, Sony will manufacture and produce four different game consoles in two generations of products: PS4, PS4 pro, ps5 and ps5 digital version, so as to maximize production efficiency. In view of the strategic significance of ps5 to Sonys market in the next decade, mugenjin factory will also become another huge asset and competitive chip of Sony.
Sonys cash cow: Playstation
What is the first thing that comes to mind when you hear the name Sony? transistor radio? Walkman? Or robot dog? If you are a loyal supporter of video games, the answer may be Playstation (PS).
Every console is precision manufactured, every part is necessary, every design has its purpose, and PS has no redundant design. Yasuhiro ootori, head of Sonys mechanical design department, once said, "if you pursue technology, mechanical equipment can become an aesthetics."
In 1994, the first PS was born. Through CD-ROM HD video games, Sony overturned Nintendo, which once dominated the home video game market, and PS became Sonys cash cow. In 2008, the collapse of Lehman Brothers caused the financial crisis. Although Sony also suffered a heavy blow, it was PS business that made it survive the crisis.

The Playstation 4 currently produced by mugengjin factory made its debut in 2013. In addition to games, it is also a platform for movies and music, and can even be used for virtual reality games.
Despite the popularity of smartphone app games, the sales volume of PS4 has steadily increased to more than 100 million once it is launched. Compared with its peers, it reached this milestone in the shortest time - a total of about 1.2 billion software sales.
Over the past six and a half years, the PS4 has generated sales of 10 trillion yen ($93 billion) and profits of more than 1 trillion yen. In 2018 and 2019, PS became Sonys highest revenue source, exceeding its revenue in the semiconductor and financial fields.

▲ PS4
Behind the explosion: an automatic chemical plant with 32 robots
Ken Kutaragi, the father of Playstation, pushed the game console despite the opposition of other executives, and finally became the classic of Sony technology today. This is inseparable from the cooperation between Sony global manufacturing & operations (sgmo) and Sony interactive entertainment, the video game department, to continuously introduce cutting-edge technology into the factory.
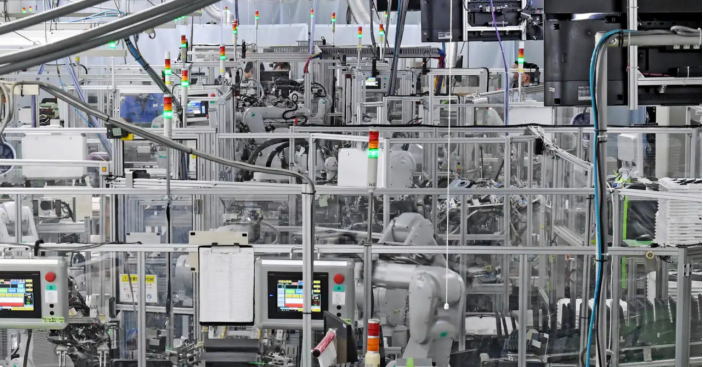
▲ internal conditions of mugengjin factory. Over the years, the factory technology has been continuously improved and transplanted to the factories of global partners
Inside the factory is a 31.4m long production line, which was completed in 2018. Now, a new game console can be produced every 30 seconds. At 31In the area of 0.4m x 6m, a total of 32 Mitsubishi Electric Industrial robots are responsible for most of the production process.
Only four workers on site are responsible for a small number of tasks. They are responsible for transporting the exposed motherboard to the production line. The other two are responsible for packaging and assembling the completed game console.
The bare motherboard is located at the starting point of the whole production line. After being sent to the assembly line by workers, the movement is realized by robots.
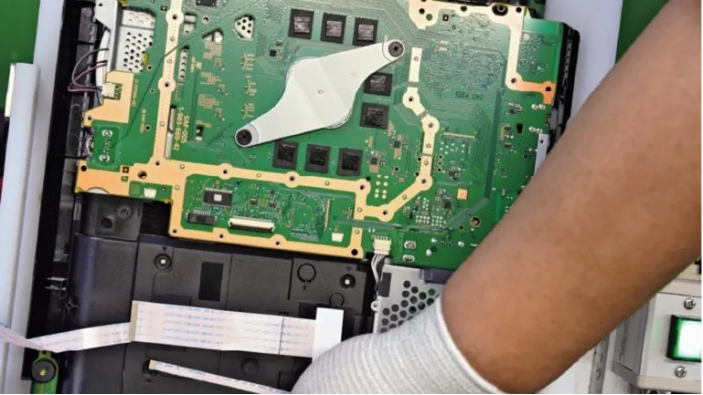
▲ main processor APU surrounded by memory chip
Soon, the white robot arm will appear from both sides of the assembly line and start connecting wires and tightening screws. They kept working like graceful dances.
Initially, the factory arranged more than 80 robots to work. After reviewing each process, they found that it was not practical at all. The current working mode is that a robot constantly repeats its actions from right to left, and cooperates with other robots to complete specific work at each point in the moving process.
They pasted various memos on various surfaces of the production line, such as the lower assembly line and the isolation around the robot. These memos record a lot of trial and error, and finally help the factory realize the automation of the whole process in 2018.
"If you look at them for a long time, they will start to look like humans," an engineer explained to the media. Unlike large robots that lift heavy objects, small robots have fine movements similar to human arms and have temperature, and "there may be no other production base to use these robots so efficiently."
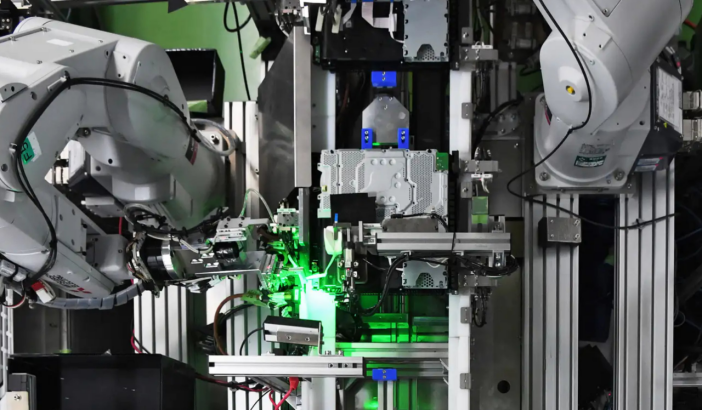
▲ the mainboard is moved by the mechanical arm
Thanks to these talented engineers, the production line can run. However, one of the factorys greatest achievements is the use of robots to connect wires, tape and other flexible parts to the console. You know, one of the biggest obstacles for musk to realize the high automation of Tesla factory is the robots inability to do anything about these soft cables. They even applied for a "structural cable" patent to solve the challenge that robots are not good at wiring, although it is easy for humans.
Of the 32 robots in Sonys factory, 26 are specialized in the installation of soft parts. Sony also designed the PS4 as small as possible so that soft foldable parts can be installed in a small space inside the game console.
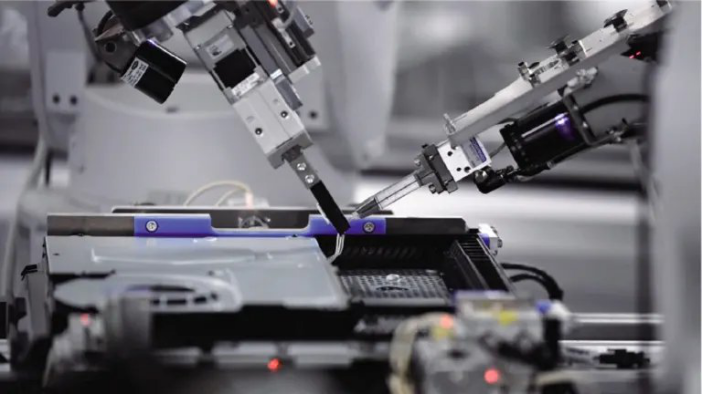
▲ among the 32 robots, 26 are specialized in the assembly of soft parts
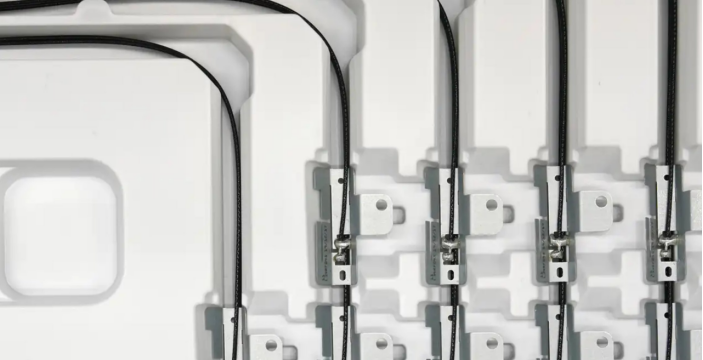
▲ PS4 is composed of many soft parts, such as antenna cable, etc. manual workers are very good at doing these jobs
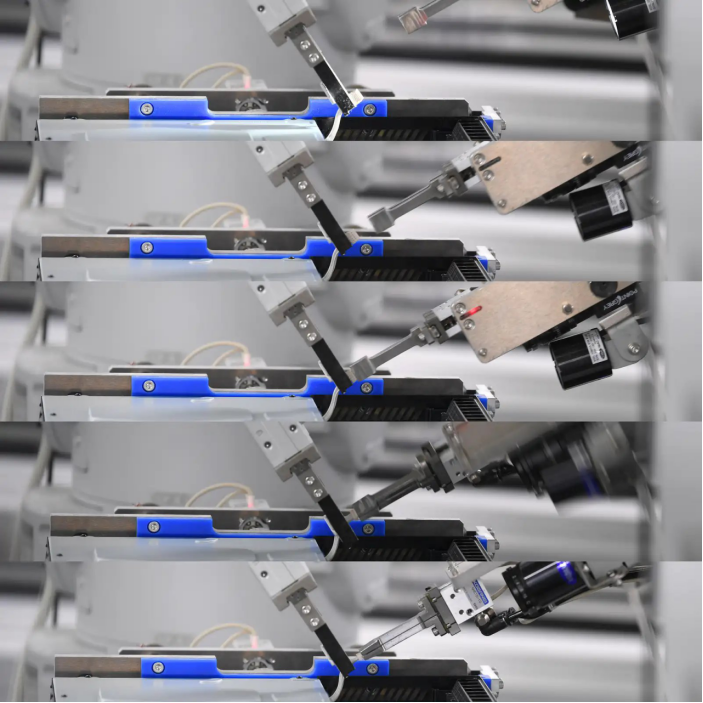
▲ the robot grabs, bends and twists the soft part with slender fingers. Then, slide this part skillfully into the connector with appropriate force
We can see in the disclosed image that one robot arm picks up a cable and holds it, and the other robot arm grabs the tip of the cable, twists it and adjusts the angle, and then puts it into the connector. The whole process emphasizes order and requires strength and precision. Human beings can do this in a short time, but it is an extremely complex operation for robots.
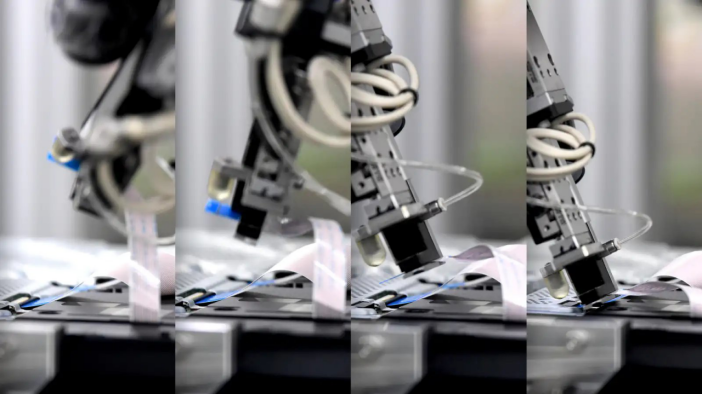
▲ the robot will twist the ribbon cable and install it into the connector
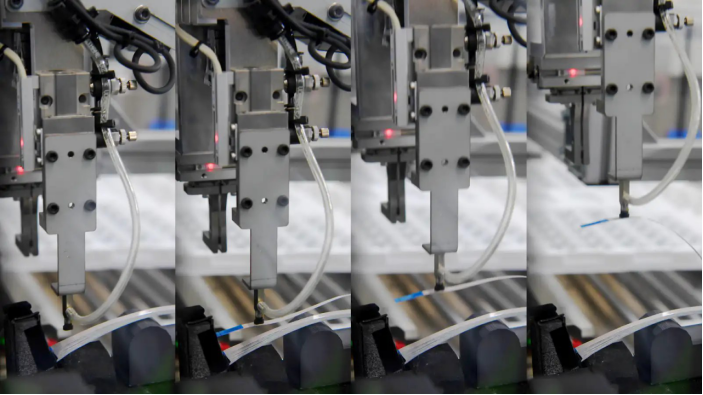
▲ for some parts that are difficult to move and grasp, the robot will first suck them up
After assembly, the assembly line sends the game console to automatic detection.
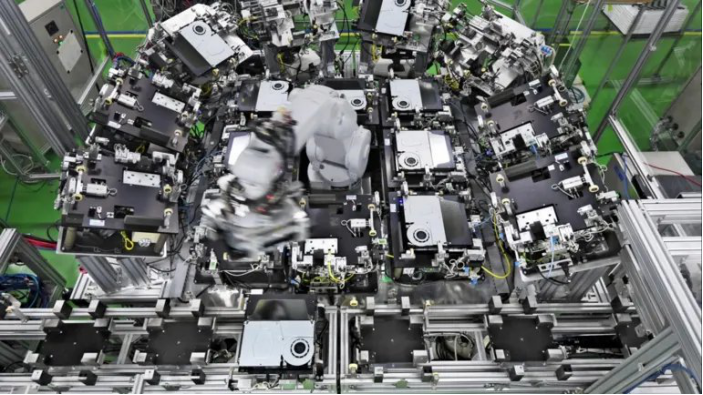
▲ a robot arm grabs the Playstation 4 game console from the assembly line and puts it on a platform for testing
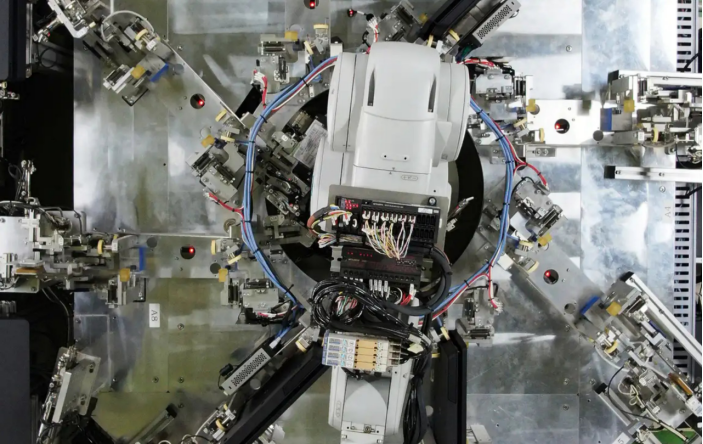
▲ carefully inspect the assembled game console
After the robot carefully checks the PS4, it can be moved away by the machine. Placing the main cover is the last step in PS4 production. The machine grabs one PS4 passing the inspection procedure at a time, puts it on the track and arranges it neatly until the main cover is installed.
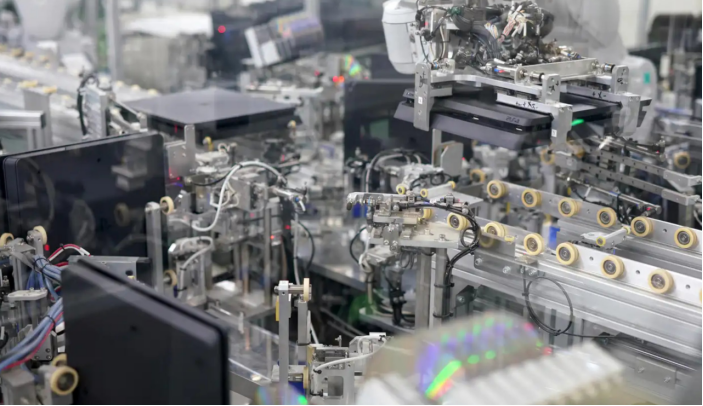
▲ the last step is to place the main engine cover

▲ one PS4 goes offline every 30 seconds
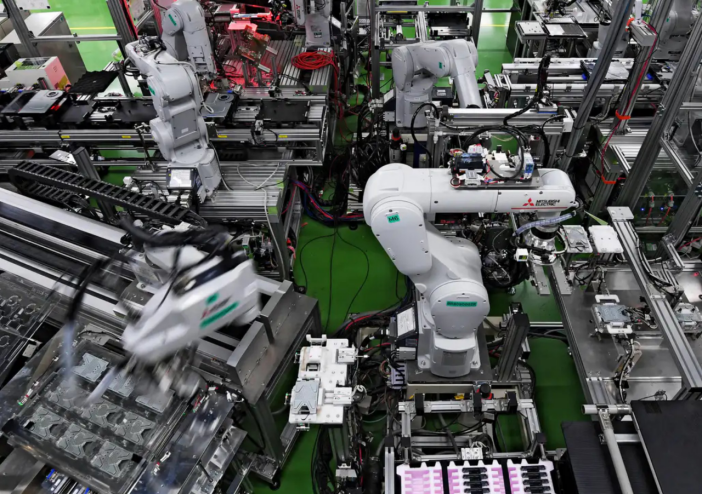
▲ 32 robots seem to work independently, but in fact they are interconnected
Sony manufacturing keeping pace with the times
In addition to the beginning and end, the whole process is highly automated. Sony is enjoying a return on its investment in a reasonable combination of robots and human labor.
"I created a profitable production line," said Hiroyuki Kusakabe, chief architect of sgmo.
When the market life of a game console is coming to an end, it will inevitably become a victim of falling sales and price competition. By continuously improving the production line, accelerating production speed and reducing costs, the production line can remain profitable.
In fact, since Sony launched its first model in 1994, mugenjin factory has carried DNA focusing on productivity. When designing, game console designer teiyu goto focused on creating a game console that is easy to mass produce. He even pushed the engineers in the factory to continuously improve production efficiency, and these fine production technologies were even transplanted to the contract manufacturing factory.

From a larger social and economic background, Sony factorys investment in automation is also to deal with the problems brought by labor costs. Labor cost is still an important chip in competition. In the past, a very important factor to reduce the production cost of these electronic products was to migrate production and manufacturing and obtain cheap labor. For example, in the early 20th century, Sony established close ties with Chinas electronic manufacturing service provider (EMS) to engage in PS production.
However, automation has changed the way companies compete ?, manufacturing itself is becoming the trigger of enterprise innovation.