Fan Cheng The international top magazine released the palm movable flexible clamping claw, whi
Published on:2020-07-08
End effector is a very important part of robot manipulator, so researchers have developed many topics for its research. Recently, a research published in the International Journal of robot research, the top international journal of robot, comes from the University of Florida, the University of science and technology design of Singapore Researchers at Columbia University jointly proposed a newly designed soft gripper with active palm. The design highlight of the gripper is the movable control of the palm (few researchers design the palm of the gripper as a movable gripper).

The researchers pointed out in the paper that with the help of the movable palm and only the open-loop grasping control, the flexible gripper can grasp dozens of objects of different shapes and sizes. The maximum weight of items that can be grabbed can reach 3kg. At the same time, the flexible gripper has good grasping stability. When the manipulator moves with an acceleration of 15m / S ^ 2, the object is still firmly grasped and does not fall.
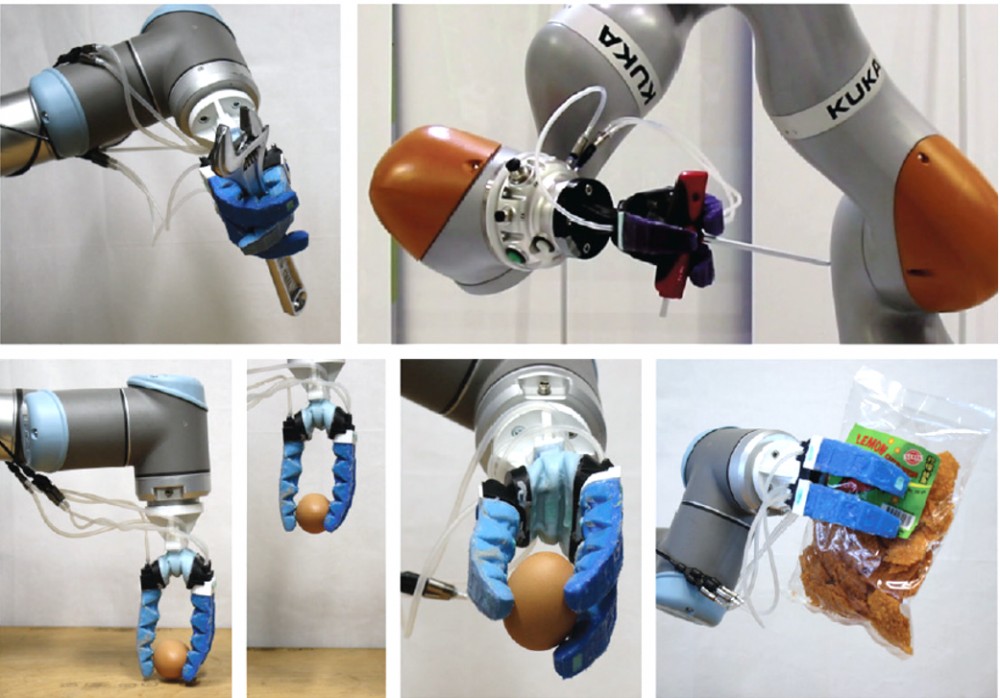
Flexible gripper with movable palm for powerful grasping
If we want robots to really enter our lives and serve the public, excellent and reliable grasping ability is obviously very important. Grabbing, a seemingly simple action that everyone can do, is a troublesome thing for robots. Robot gripper can be said to be an essential key component of the manipulator. It is like a human hand. As the end effector of the manipulator, the gripper directly contacts with the surrounding environment of the robot to perform the tasks of grasping, transferring and operating objects. The effective and powerful gripper can improve the grasping performance and the ability of operating objects of the robot. The more popular and practical clamping claws are two finger and three finger clamping claws. They have simple structure and reliable grasping. Relatively speaking, although the five finger humanoid manipulator is flexible and highly bionic, there is no doubt that too many degrees of freedom also make the motion planning of grasping particularly difficult.
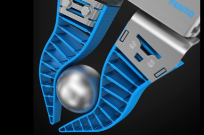
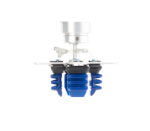
Several common manipulators: FESTO fishbone bionic gripper, SRT Beijing soft robot circumferential adjustable installation gripper
In order to improve the grasping performance of the manipulator, most researchers focus on how to design better and more flexible fingers. However, some researchers find another way to seek answers from other aspects, such as making the "palm", a neglected part, movable. Today, Id like to introduce a new flexible gripper developed by scientists. Researchers from the University of Florida, Singapore University of technology and design and Columbia University jointly proposed a newly designed soft gripper with active palm, which was published in the International Journal of robotic research, a top international journal of robotics. The design highlight of the gripper is the movable control of the palm.
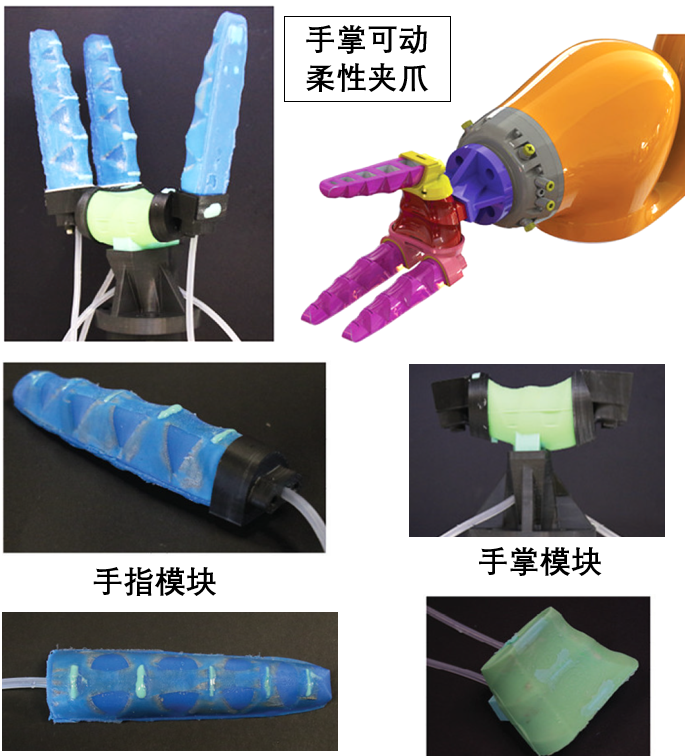
Palm movable flexible clamping claw
If an ordinary flexible gripper is given a movable palm, it is equivalent to adding an additional degree of freedom for the gripper. The movable palm can effectively expand the grasping range of the gripper. Specifically, activating the palm when grasping small objects can reduce the gap between fingers, so as to realize grasping. Activating the palm when grasping large objects can increase the grasping force and make the grasping more stable. Well, I have to say that this idea is really great!
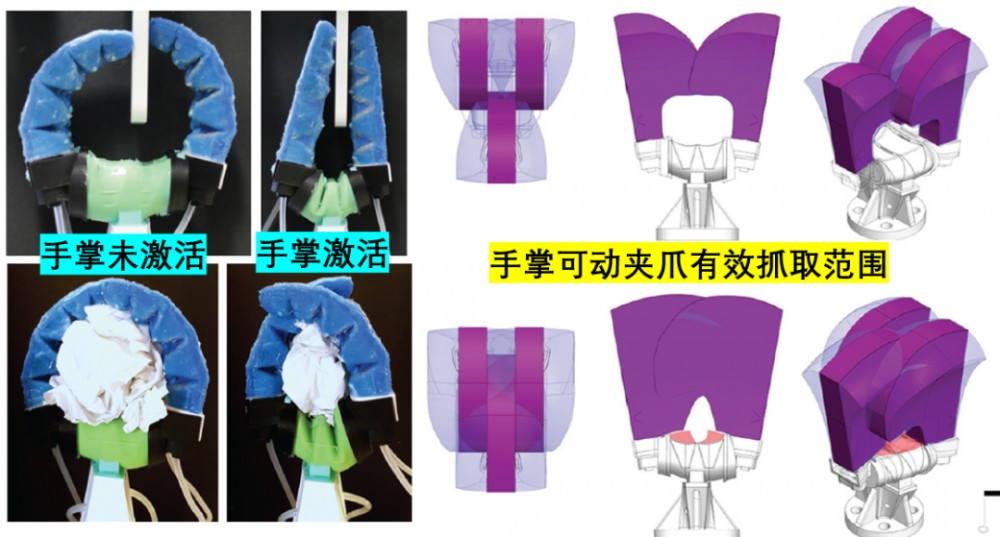
The movable palm expands the gripping range of the clamping claw
As shown in the figure, the researchers designed a 3-finger flexible gripper. Both fingers and palm are driven by vacuum. Compared with positive pressure drive, the vacuum driven flexible gripper is safe, reliable, low material loss and long service life. The researchers pointed out in the paper that with the help of the movable palm and only the open-loop grasping control, the flexible gripper has excellent compatibility with objects of different shapes, sizes and weights. It can grasp dozens of different objects. The maximum weight of items that can be grabbed can reach 3kg. At the same time, the flexible gripper has good grasping stability.
According to the authors introduction in the paper, like other flexible grippers, the flexible gripper can grasp some fragile and fragile items, such as eggs, bagged potato chips, and goblets. At the same time, with the help of the movable palm structure, it can also grasp heavy items, such as large wrenches and 2L soda (this is difficult for most flexible grippers). Lets first enjoy the grasping performance of this flexible gripper (a complete video is attached at the end of the article). In the next section, the design and some performance tests of this flexible gripper will be introduced in detail. The basic information of the paper is also attached at the end of the paper.

Grab bread
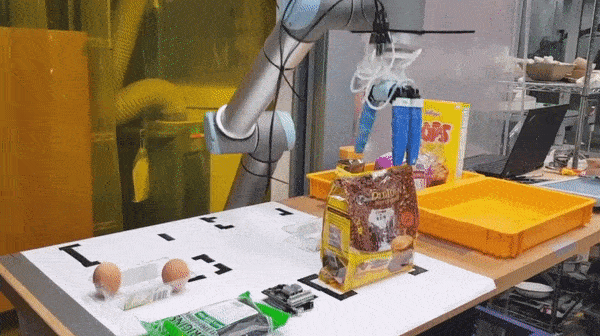
Grab a bag of coffee
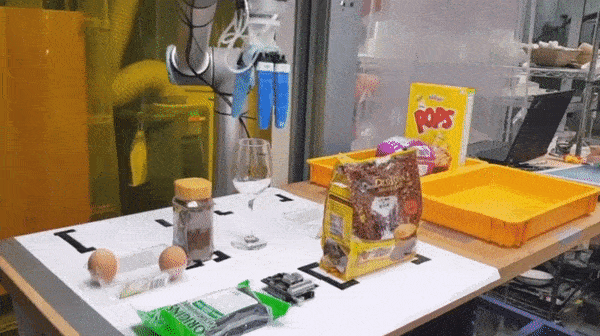
Grab the glass
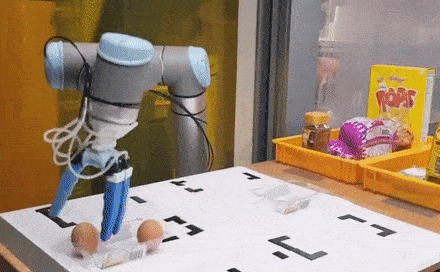
Grab an egg
In the paper, the researchers showed that the flexible gripper they designed can grasp more than 20 kinds of objects in different forms, from small ball point pens to flat optical discs, as well as eggs, fruits and other common daily necessities, such as wine glasses, water bottles and so on. Basically, theres only what you cant think of, and theres nothing it cant catch (a little exaggeration).
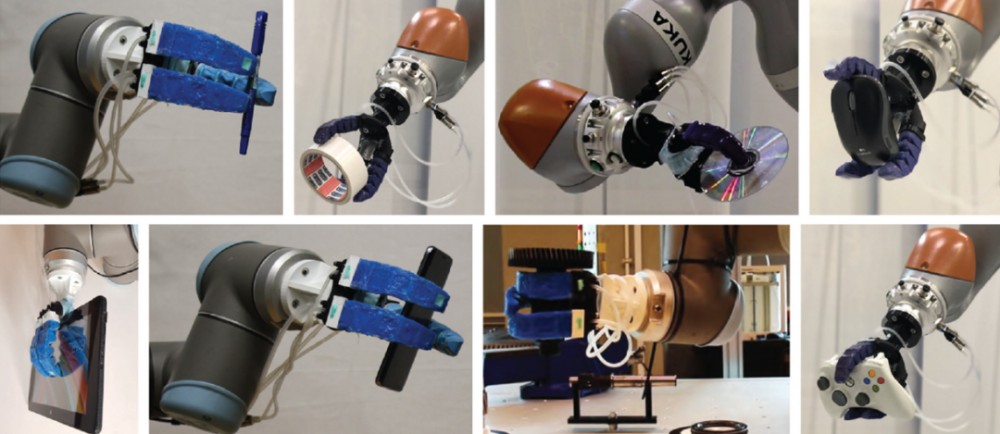
Capture diversity display 1

Capture diversity display 2
This flexible gripper is not only compatible with grasping many different items, but also inferior to the hard gripper in terms of grasping repeatability, accuracy and stability. The following two dynamic diagrams show the repeatability and stability test of the flexible gripper. When the manipulator moves with an acceleration of 15m / S ^ 2, the object is still firmly held and does not fall.

Grab repeatability test
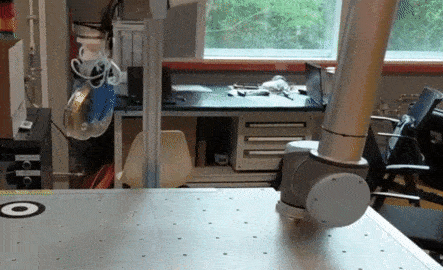
Grab stability test
The flexible finger is driven by vacuum. When designing the flexible finger, the researchers adopted the joint structure design. Inside the finger, there are five wedge-shaped blocks as joints, which are made of hard soft glue. The wedge-shaped block is wrapped in a soft, thin, almost elastic air tight film, which ensures that the fingers can not elongate, but does not affect the bending deformation of the fingers. When the air inside the finger is gradually extracted, the finger will bend and deform.
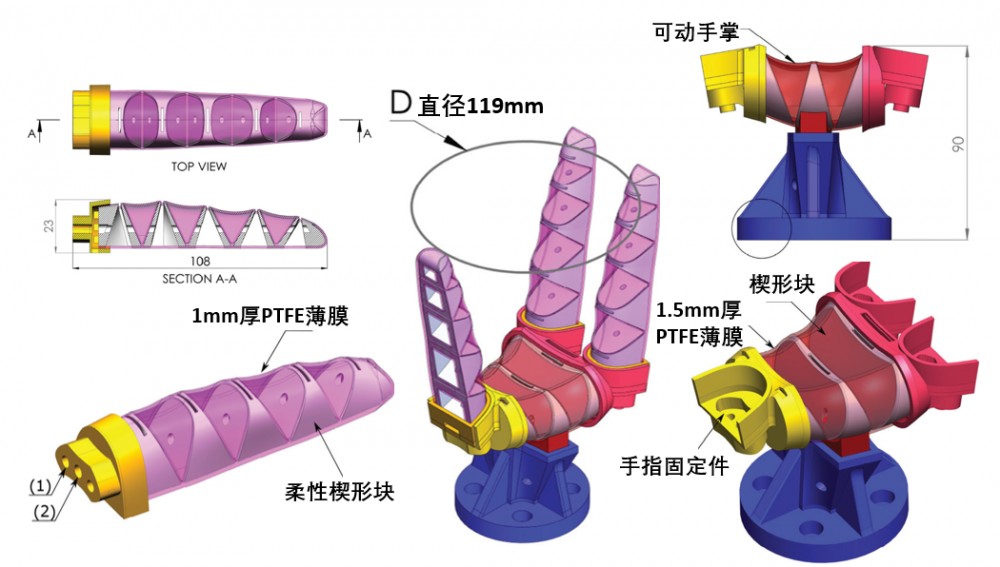
Three dimensional drawing of flexible gripper design
The design of the palm is similar to that of a finger. It is also composed of an internal wedge and an external elastic film. There are three wedge-shaped blocks in the palm. When the palm is vacuumized, the wedge-shaped blocks will be close to each other, resulting in the deformation of the palm. The processing method of palm and finger is similar, first inject the flexible film outside the mold, then inject the wedge block inside the mold, and finally assemble them and seal them.
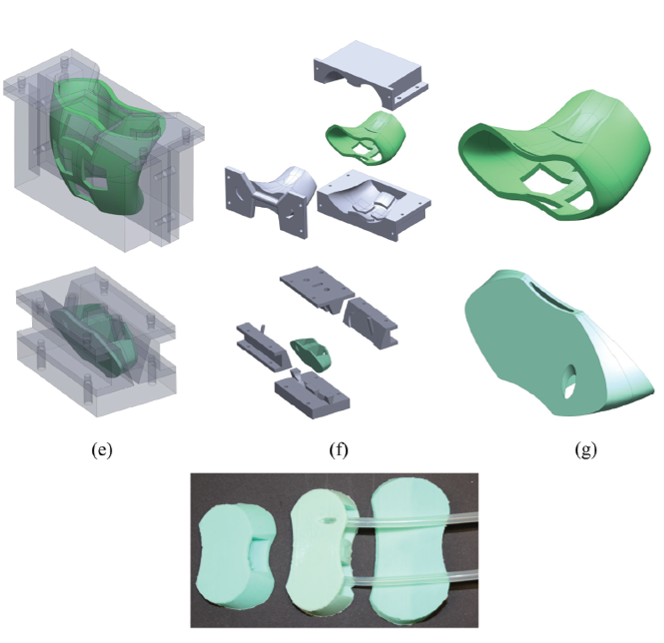
Injection molding process of palm
Through the test results, it is obvious that the effective grasping range of the flexible gripper changes greatly when the palm is activated and inactive. This also proves to some extent that the simple structure of movable palm is very helpful to improve the grasping ability.

Display of palm movable grasping and palm stationary grasping
The researchers tested the load of flexible fingers and made flexible films of different materials. Under the same negative pressure (- 98. 3kpa). According to the experimental results, the researchers finally selected a material called moldstar30 as the material of finger coating film.
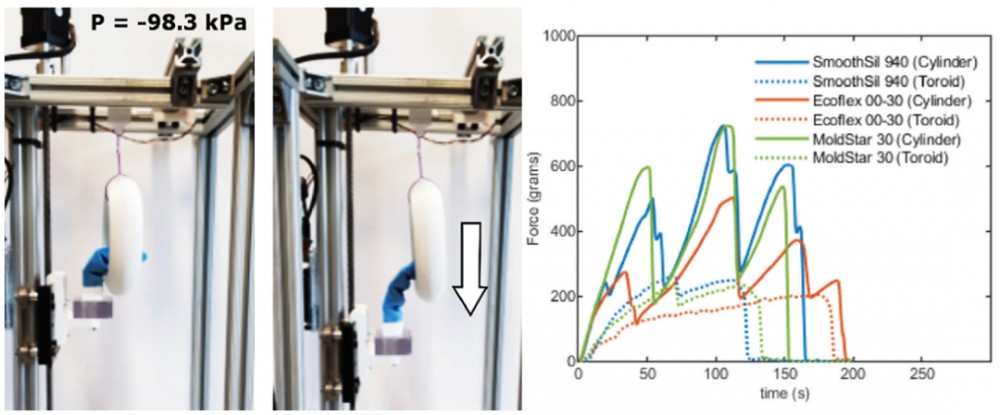
Finger tension test
In order to better characterize the grasping effect of the movable palm structure, the researchers carried out the grasping load test. The specific test method is to make the flexible gripper grasp the cylindrical object, and then pull out the object from two directions (along the finger direction and perpendicular to the finger direction). The greater the required tension, the better and more stable the grasping effect. It can be seen that when the palm is movable, the gripping force of the clamping claw is much higher than that of the immovable palm, and the maximum gap can be about 15N (the unit of force in the figure is grams). That is, the grasping ability of the palm movable gripper is more than twice that of the ordinary flexible gripper.
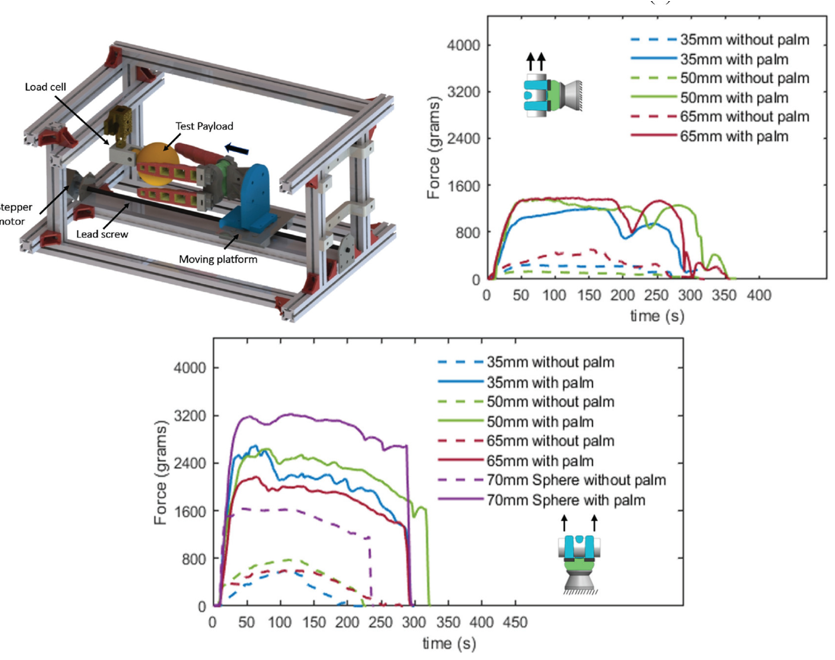
Grip test
For mechanical grippers, load capacity and grasping adaptability are very important indicators. For most of the current flexible grippers, it is difficult to have both. In addition, fast and stable grasping is also a great challenge for the flexible gripper. The flexible gripper with vacuum drive and movable palm introduced today takes into account the above problems, and realizes the grasping effect of large load and compatibility. At the same time, this gripper can also realize stable and reliable grasping, which is of great significance for the development of flexible gripper in practical application.
The researchers pointed out that the flexible gripper they designed can be easily installed on the manipulator, such as KUKA, ur10, etc. Only through open-loop control, we can grasp objects with different shapes, hardness and weight. In future research, researchers hope to add closed-loop control to measure the deformation and contact stress of fingers and palms, so as to achieve more stable and reliable grasping.

The researchers pointed out in the paper that with the help of the movable palm and only the open-loop grasping control, the flexible gripper can grasp dozens of objects of different shapes and sizes. The maximum weight of items that can be grabbed can reach 3kg. At the same time, the flexible gripper has good grasping stability. When the manipulator moves with an acceleration of 15m / S ^ 2, the object is still firmly grasped and does not fall.
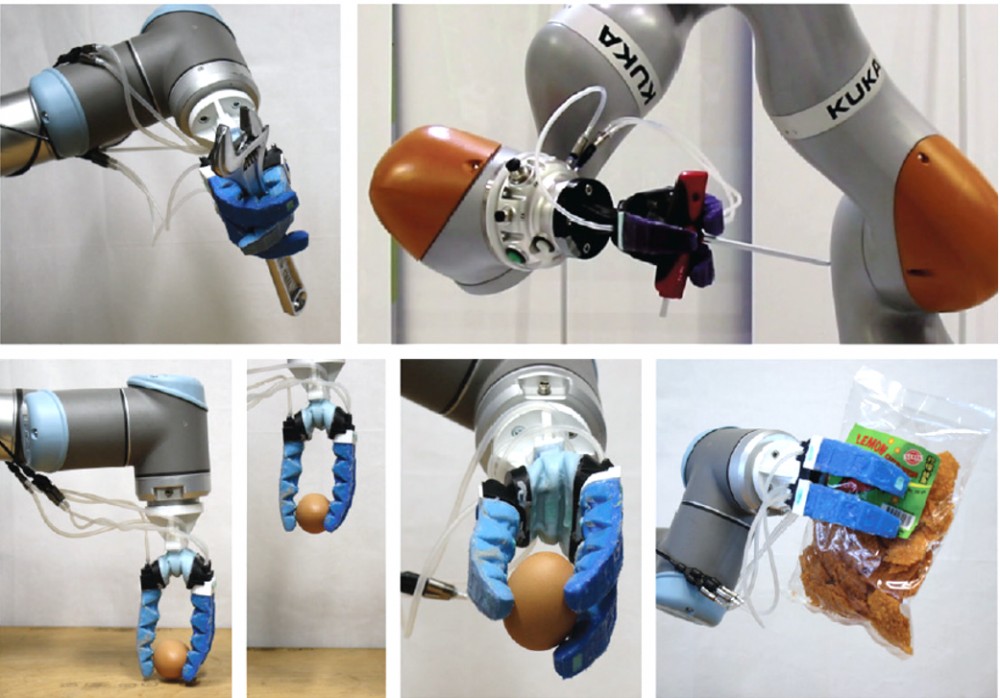
Flexible gripper with movable palm for powerful grasping
If we want robots to really enter our lives and serve the public, excellent and reliable grasping ability is obviously very important. Grabbing, a seemingly simple action that everyone can do, is a troublesome thing for robots. Robot gripper can be said to be an essential key component of the manipulator. It is like a human hand. As the end effector of the manipulator, the gripper directly contacts with the surrounding environment of the robot to perform the tasks of grasping, transferring and operating objects. The effective and powerful gripper can improve the grasping performance and the ability of operating objects of the robot. The more popular and practical clamping claws are two finger and three finger clamping claws. They have simple structure and reliable grasping. Relatively speaking, although the five finger humanoid manipulator is flexible and highly bionic, there is no doubt that too many degrees of freedom also make the motion planning of grasping particularly difficult.
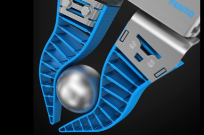
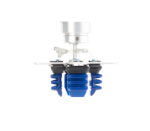
Several common manipulators: FESTO fishbone bionic gripper, SRT Beijing soft robot circumferential adjustable installation gripper
In order to improve the grasping performance of the manipulator, most researchers focus on how to design better and more flexible fingers. However, some researchers find another way to seek answers from other aspects, such as making the "palm", a neglected part, movable. Today, Id like to introduce a new flexible gripper developed by scientists. Researchers from the University of Florida, Singapore University of technology and design and Columbia University jointly proposed a newly designed soft gripper with active palm, which was published in the International Journal of robotic research, a top international journal of robotics. The design highlight of the gripper is the movable control of the palm.
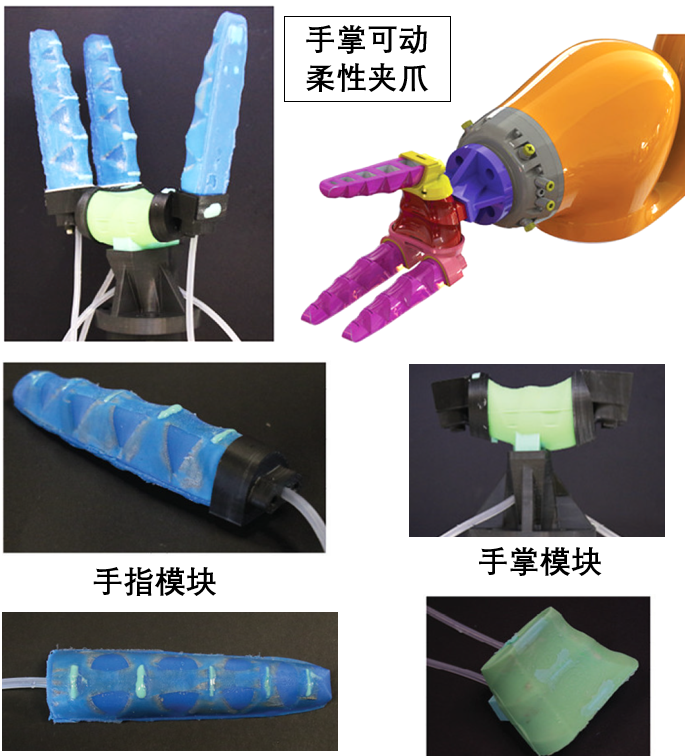
Palm movable flexible clamping claw
If an ordinary flexible gripper is given a movable palm, it is equivalent to adding an additional degree of freedom for the gripper. The movable palm can effectively expand the grasping range of the gripper. Specifically, activating the palm when grasping small objects can reduce the gap between fingers, so as to realize grasping. Activating the palm when grasping large objects can increase the grasping force and make the grasping more stable. Well, I have to say that this idea is really great!
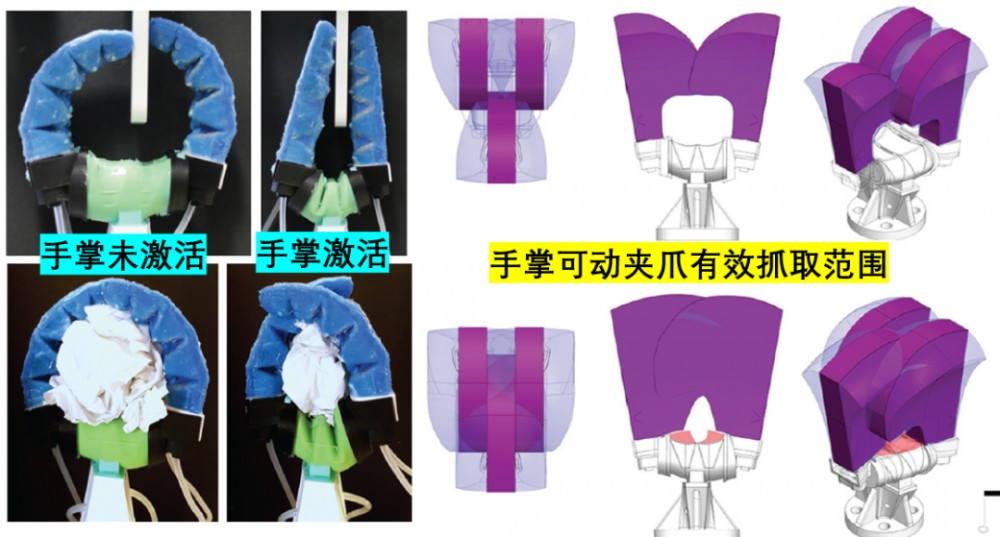
The movable palm expands the gripping range of the clamping claw
As shown in the figure, the researchers designed a 3-finger flexible gripper. Both fingers and palm are driven by vacuum. Compared with positive pressure drive, the vacuum driven flexible gripper is safe, reliable, low material loss and long service life. The researchers pointed out in the paper that with the help of the movable palm and only the open-loop grasping control, the flexible gripper has excellent compatibility with objects of different shapes, sizes and weights. It can grasp dozens of different objects. The maximum weight of items that can be grabbed can reach 3kg. At the same time, the flexible gripper has good grasping stability.
According to the authors introduction in the paper, like other flexible grippers, the flexible gripper can grasp some fragile and fragile items, such as eggs, bagged potato chips, and goblets. At the same time, with the help of the movable palm structure, it can also grasp heavy items, such as large wrenches and 2L soda (this is difficult for most flexible grippers). Lets first enjoy the grasping performance of this flexible gripper (a complete video is attached at the end of the article). In the next section, the design and some performance tests of this flexible gripper will be introduced in detail. The basic information of the paper is also attached at the end of the paper.

Grab bread
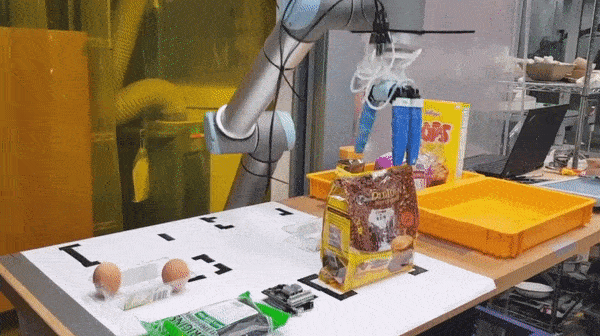
Grab a bag of coffee
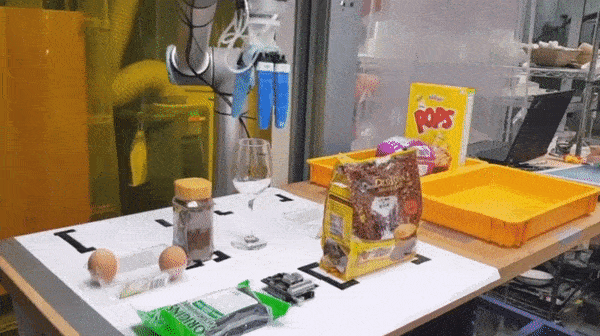
Grab the glass
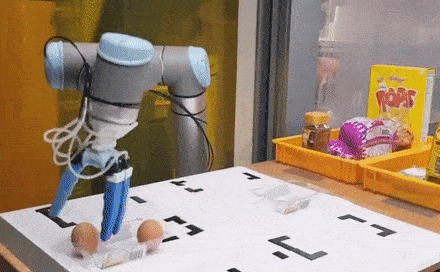
Grab an egg
In the paper, the researchers showed that the flexible gripper they designed can grasp more than 20 kinds of objects in different forms, from small ball point pens to flat optical discs, as well as eggs, fruits and other common daily necessities, such as wine glasses, water bottles and so on. Basically, theres only what you cant think of, and theres nothing it cant catch (a little exaggeration).
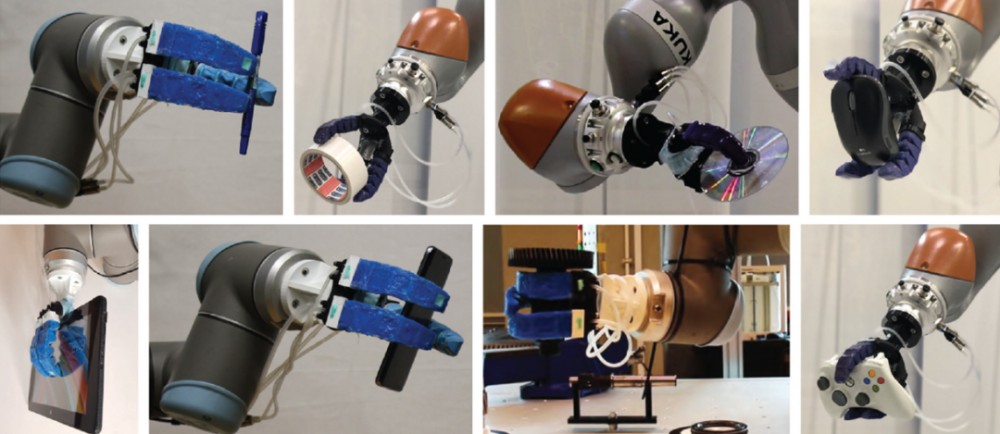
Capture diversity display 1

Capture diversity display 2
This flexible gripper is not only compatible with grasping many different items, but also inferior to the hard gripper in terms of grasping repeatability, accuracy and stability. The following two dynamic diagrams show the repeatability and stability test of the flexible gripper. When the manipulator moves with an acceleration of 15m / S ^ 2, the object is still firmly held and does not fall.

Grab repeatability test
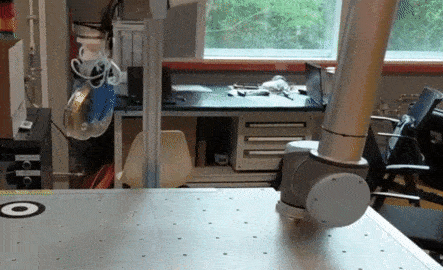
Grab stability test
The flexible finger is driven by vacuum. When designing the flexible finger, the researchers adopted the joint structure design. Inside the finger, there are five wedge-shaped blocks as joints, which are made of hard soft glue. The wedge-shaped block is wrapped in a soft, thin, almost elastic air tight film, which ensures that the fingers can not elongate, but does not affect the bending deformation of the fingers. When the air inside the finger is gradually extracted, the finger will bend and deform.
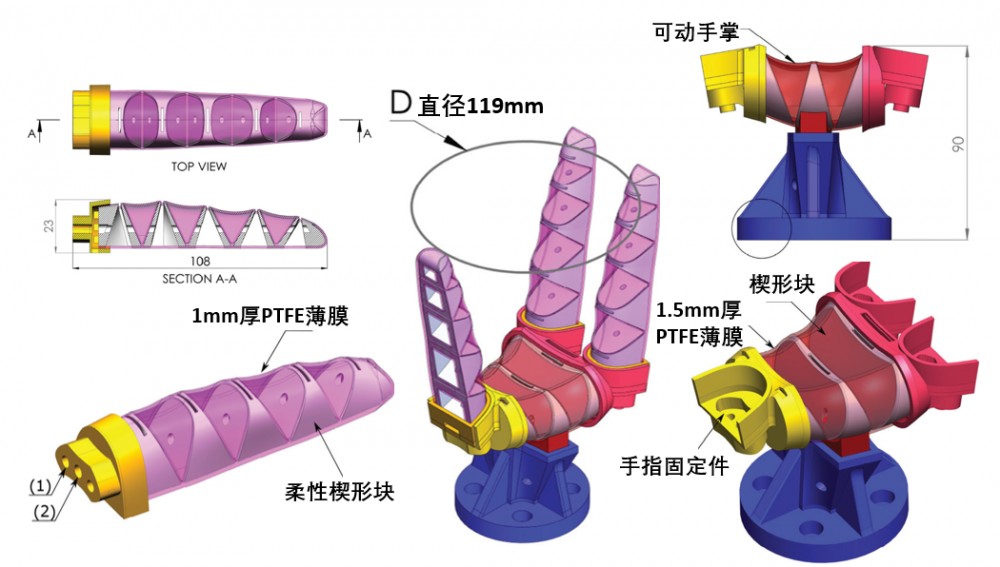
Three dimensional drawing of flexible gripper design
The design of the palm is similar to that of a finger. It is also composed of an internal wedge and an external elastic film. There are three wedge-shaped blocks in the palm. When the palm is vacuumized, the wedge-shaped blocks will be close to each other, resulting in the deformation of the palm. The processing method of palm and finger is similar, first inject the flexible film outside the mold, then inject the wedge block inside the mold, and finally assemble them and seal them.
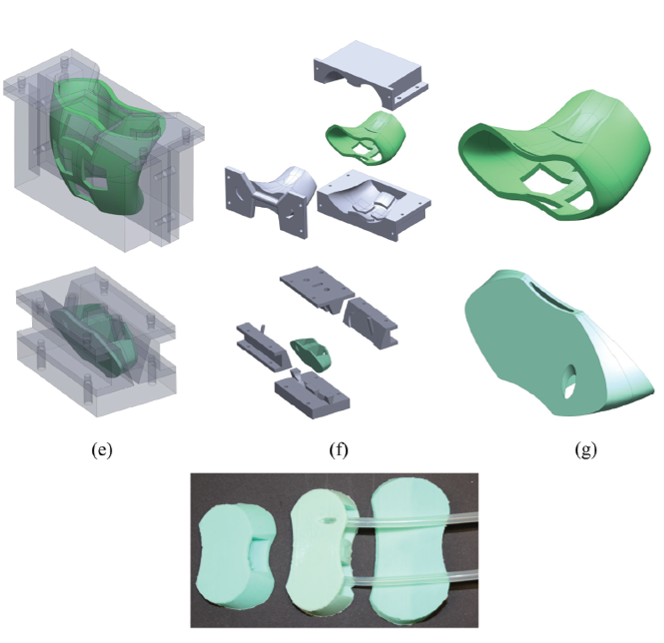
Injection molding process of palm
Through the test results, it is obvious that the effective grasping range of the flexible gripper changes greatly when the palm is activated and inactive. This also proves to some extent that the simple structure of movable palm is very helpful to improve the grasping ability.

Display of palm movable grasping and palm stationary grasping
The researchers tested the load of flexible fingers and made flexible films of different materials. Under the same negative pressure (- 98. 3kpa). According to the experimental results, the researchers finally selected a material called moldstar30 as the material of finger coating film.
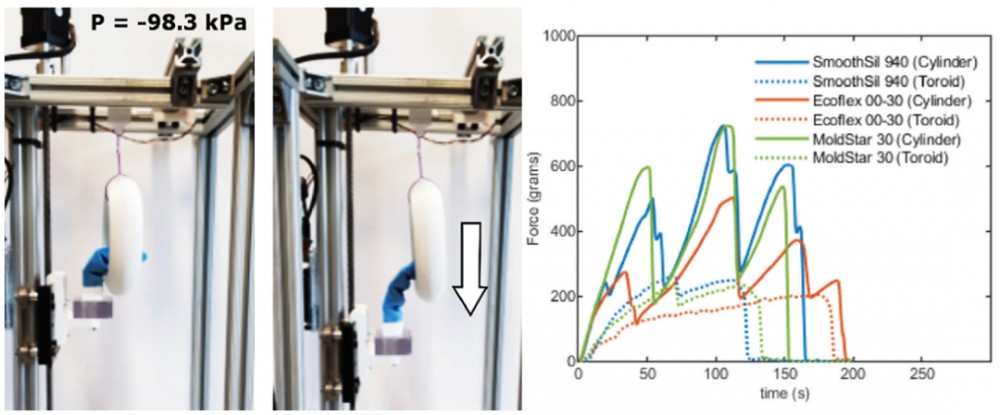
Finger tension test
In order to better characterize the grasping effect of the movable palm structure, the researchers carried out the grasping load test. The specific test method is to make the flexible gripper grasp the cylindrical object, and then pull out the object from two directions (along the finger direction and perpendicular to the finger direction). The greater the required tension, the better and more stable the grasping effect. It can be seen that when the palm is movable, the gripping force of the clamping claw is much higher than that of the immovable palm, and the maximum gap can be about 15N (the unit of force in the figure is grams). That is, the grasping ability of the palm movable gripper is more than twice that of the ordinary flexible gripper.
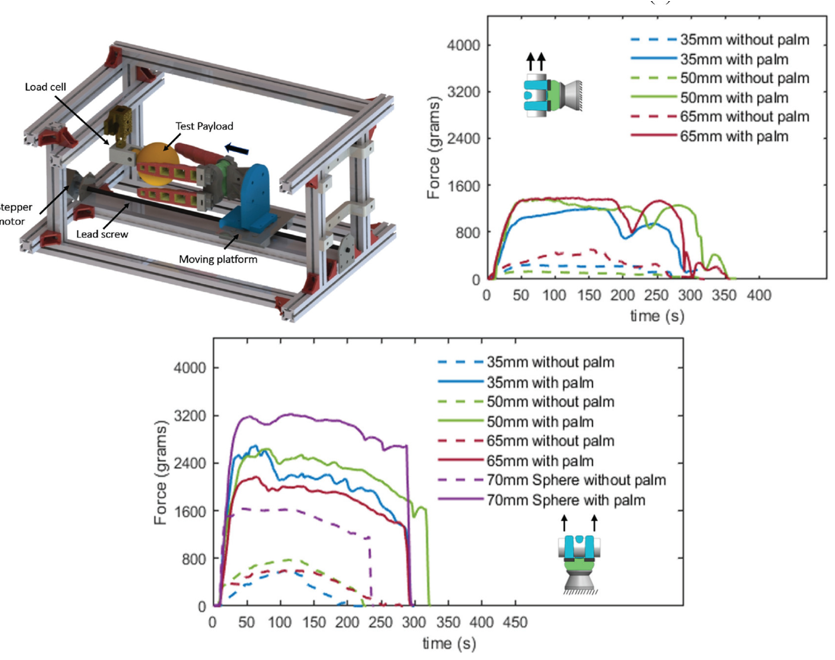
Grip test
For mechanical grippers, load capacity and grasping adaptability are very important indicators. For most of the current flexible grippers, it is difficult to have both. In addition, fast and stable grasping is also a great challenge for the flexible gripper. The flexible gripper with vacuum drive and movable palm introduced today takes into account the above problems, and realizes the grasping effect of large load and compatibility. At the same time, this gripper can also realize stable and reliable grasping, which is of great significance for the development of flexible gripper in practical application.
The researchers pointed out that the flexible gripper they designed can be easily installed on the manipulator, such as KUKA, ur10, etc. Only through open-loop control, we can grasp objects with different shapes, hardness and weight. In future research, researchers hope to add closed-loop control to measure the deformation and contact stress of fingers and palms, so as to achieve more stable and reliable grasping.